energy-based plane-strain compression test|plane strain testing methods : discounter plane-strain compression test data for sand for a range of confining pressures from very low levels to approximately 196 kPa. . that a minimum energy ratio at failure is achieved. De Josselin de Jong (1976) put the theory on more solid basis by . is chosen based on the observations that, for a particular type of Gostaríamos de exibir a descriçãoaqui, mas o site que você .
{plog:ftitle_list}
previlab.com.br
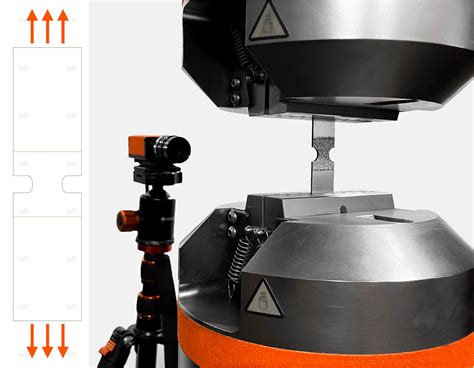
In this paper, we develop a simple correlation between peak friction angle, critical-state friction angle, and dilatancy based on triaxial compression and plane-strain compression test data .One variation of the test is also known as the Watts-Ford test. It is an engineering test, and is a particularly specialized way of determining some of the material characteristics of the metal being tested, and its specialization can be summarized by this quote: The test is useful when the sheet pieces are too small for a tensile test of a balanced biaxial test. It can give stress-strain curves up to considerably higher strains than tensile tests.One variation of the test is also known as the Watts-Ford test. It is an engineering test, and is a particularly specialized way of determining some of the material characteristics of the metal being tested, and its specialization can be summarized by this quote: The test is useful when the sheet pieces are too small for a tensile test of a balanced biaxial test. It can give stress-strain curves up to considerably higher strains than tensile tests.1.1 These test methods are designed to characterize the toughness of plastics in terms of the critical-stress-intensity factor, KIc, and the energy per unit area of crack surface or critical .
plane-strain compression test data for sand for a range of confining pressures from very low levels to approximately 196 kPa. . that a minimum energy ratio at failure is achieved. De Josselin de Jong (1976) put the theory on more solid basis by . is chosen based on the observations that, for a particular type ofMeasuring the compressive strength of a steel drum. In mechanics, compressive strength (or compression strength) is the capacity of a material or structure to withstand loads tending to reduce size (compression).It is . Plane strain compression tests were used to study the deformation behavior of an Inconel 625 alloy sheet at various temperatures and strain rates. The peak stress was selected to establish the constitutive . The other group is derived from the mechanical property of rock obtained via uniaxial and triaxial compression tests, e.g., BIs based on strength/stress parameters, which can be expressed by the compressive/tensile strength or characteristic stress on rock stress–strain curves (Guo et al. 2015; Kahraman and Altindag 2004; Özfırat et al .
When the material is under compression, the forces on the ends are directed towards each other producing a compressive stress resulting in a compressive strain (Figure \(\PageIndex{2}\)). For compressive strains, if we define \(\delta l=l_{0}-l>0\) then Equation \ref{26.2.3} holds for compressive stresses provided the compressive stress is not .Material failure theory is an interdisciplinary field of materials science and solid mechanics which attempts to predict the conditions under which solid materials fail under the action of external loads.The failure of a material is usually classified into brittle failure or ductile failure ().Depending on the conditions (such as temperature, state of stress, loading rate) most materials can .
plane strain testing methods
The in-plane compression response and energy absorption capacity of a new foam filled re-entrant honeycomb (FFRH) with negative Poisson’s ratio were investigated in this paper. Polyurethane foam filled aluminum alloy re-entrant honeycomb structures were fabricated though 3D printing method and pressure foaming method. The in-plane compression .Two types of experiments, axisymmetrical compression (UC) and plane strain compression (PSC) tests were performed using the carbon-manganese steel with the chemical composition given in Table 12.7.The conditions were the same for the both types of tests, three temperatures of 900 °C, 1000 °C and 1100 °C and three strain rates of 0.1 s- 1, 1 s- 1 and 10s- 1. geometries in both uniaxial compression and standard plane strain compression tests, and an additional simulation of a modified plane strain compression test sample geometry, designed to provide more uniform strain distributions, is also performed. A user routine is incorporated into the model to predict the localized Fig. 4 shows the three different ways to perform an out-of-plane axial compression test. A full-cell compression, during which the cell is fully covered by two rigid plates, is the closest to an ideal uniaxial compression. The challenge to applying a full-cell compression test is the high force level.
Impact of specimen thickness on fracture toughness. In materials science, fracture toughness is the critical stress intensity factor of a sharp crack where propagation of the crack suddenly becomes rapid and unlimited. A component's thickness affects the constraint conditions at the tip of a crack with thin components having plane stress conditions and thick components having . For this purpose, plane strain compression was adopted to simulate the rolling conditions in the present paper. The so-called plane strain compression means that in the test, a metal plate is placed between two strip-like anvils that produce a groove across its width, meanwhile the length of the plate is promoted and the width is constrained [15].
High-temperature plane-strain compression of a Ti-6Al-2Sn-4Zr-2Mo (Ti-6242) alloy with a lamellar structure was applied by a thermal simulation machine Gleeble 3800 at a temperature of 1223-1370 K and a strain rate of 0.01-10 s−1. Constitutive relations between the flow stress and strain at different temperatures and strain rates were constructed based on . Specially designed material test jigs were developed for the plane strain compression tests and for simple shear tests. Fig. 2 is the schematic illustration of the plane strain compression test. As for the plane strain compression test jig, the width of upper and lower punches was the 3.0 mm. The current assisted plane strain compression (CAPSC) test was proposed as the physical simulation test for CAFS, and the air cooling method was used to eliminate the effect of Joule heat. The CAPSC tests and the FE simulations of 30CrMnSiA were carried out, and the influences of peak current density and duty ratio on flow behavior were analysed.
Results and discussions. Figure 4 illustrates the triaxial compression deviatoric stress–strain curve of weak structural plane rock mass under various dip angles. The analysis demonstrates that .In view that the traditional dynamic recrystallization (DRX) model cannot effectively predict the DRX process in the hot deformation process of sheet metal, DRX behavior modeling and simulation of q890 steel plate based on the .tensile test. It is based on the plane-strain compression test, initially developed by Green, and is suitable for large strains. The experimental investigation of plane-strain compression test is carried out on Polymethylmethacrylate (PMMA) in the form of a flat plate, over a wide range of
3.1.2 critical strain energy release rate, G Ic,n—toughness parameter based on energy required to fracture. See 3.1.5 for reference to additional definition. 3.1.3 plane-strain fracture toughness, K Ic,n—toughness parameter indicative of the resistance of a material to fracture. See 3.1.5 for reference to additional definition. Although there are methods for testing the stress-strain relation and strength, which are the most fundamental and important properties of metallic materials, their application to small-volume materials and tube components is limited. In this study, based on energy density equivalence, a new dimensionless elastoplastic load-displacement model for compressed .
plane strain stress testing
Hot/Warm Deformation: Plane strain compression test. In single- or multiple hit compression tests, strain and strain rate are controlled separately yet synchronously using the optional Hydrawedge®. Strip Annealing Process Simulation: Both batch and continuous annealing processes can be simulated using a strip annealing jaw system.
where W dev is the deviatoric third-order deformation form strain energy function, C 10 is a material constant and I 1 is the first invariant of the left Cauchy–Green deformation tensor.. The Neo-Hookean model is based on the statistical thermodynamics of cross-linked polymer chains. Cross-linked polymers work in a manner consistent with the Neo-Hookean .
The total strain energy density is the sum of positive elastic strain energy density and plastic strain energy density. Based on the fatigue data in Table 2 , as well as the monotonic tension tests we carried out earlier, some derived mechanical and fatigue parameters of Al 7075-T6511 alloy are listed in Table 3 . To this purpose, the hypothesis was tested through virtual experiments in which a numerical simulation of a uniaxial compression test with a cylindrical, rock-like sample was created to mimic the . 1 INTRODUCTION. Rocks around deep underground openings are under a polyaxial stress state and can exhibit violent dynamic behaviour during mining operations due to unloading caused by excavation. 1-7 This sudden change in boundary conditions under high in-situ confining pressure governs the violent failure of rock, commonly known as ‘strain burst’, . The applicability of the plane strain compression test to simulate the flat rolling process is examined. analytically and through experiments. . hardened to Rc 55 and ground to have a surface finish of 1.8 ti, peak to valley. The loads are measured by a strain gauge-based loadcell; the displaccments are monitored by a DCDT. The temperatures .
A new analytical method to determine the effective tool width in contact with the sheet workpiece in the plane strain compression test, which changes during the test if a tool with a radius is used, is proposed. A detailed description of this method and the corresponding procedure of the flow curve determination for high-strength sheet steels are presented. The .

plane strain strain test
plane strain fracture
Resultado da 22 de nov. de 2023 · Copinha: veja os grupos e as sedes da edição de 2024. Competição começa no dia 2 de janeiro e termina no dia 25 do mesmo .
energy-based plane-strain compression test|plane strain testing methods